Additive manufacturing: un’alternativa ai razzi riutilizzabili? di Adriano V. Autino |
|||
Come promesso, ecco un breve resoconto, ed alcune considerazioni, sul workshop Additive Manufacturing, organizzato dall’ASI, dal 20 al 22 Luglio, nell’auditorium della sede di Tor Vergata a Roma. L’iniziativa, che ha visto fortemente impegnati Roberto Formaro (capo della Technology and Engineering Division dell’ASI), Danilo Rubini ed il loro staff, è stata decisamente un successo, ed ha visto la presenza, nei tre giorni, di più di trecento partecipanti, in grande maggioranza appartenenti al settore industriale ed al mondo accademico. Queste note sono scritte di getto, appena rientrato da Roma, spero mi perdonerete qualche omissione o imprecisione, cui magari qualche collega potrà rimediare, postando nei forum. Complessivamente hanno preso la parola una cinquantina di oratori, di cui il 60% rappresentanti realtà industriali o di ricerca tecnologica, il 30% università, il 10% enti di ricerca. Tra le università molto nutrita la presenza del Politecnico di Milano e dell’Università Tor Vergata. Mi ha un po’ sorpreso la più limitata (benchè di notevole livello) partecipazione del Politecnico di Torino, soprattutto se consideriamo la cospicua presenza al workshop di aziende torinesi. Pensavate possibile, nel contesto di questa crisi che sembra non finire mai, che potesse esistere un settore industriale, anche nel nostro paese, che cresce a due cifre? Bene, questo settore esiste, e si chiama additive manufacturing o, per dirla in italiano, fabbricazione additiva. |
|||
Tommaso Ghidini – ESA![]()
|
Durante il workshop i protagonisti del settore si sono visti in faccia, senza nascondere una certa sorpresa, nel constatare che in molti casi si sta ormai parlando di vera produzione, e non solo di prototipazione, e che componenti stampati in 3D stanno già volando. Fortemente raccomandata da parte dall’ESA, presente al workshop con Tommaso Ghidini, capo della sezione Materials Technology, si è parlato molto di standardizzazione e certificazione dei processi, passo fondamentale per l’utilizzabilità in sicurezza dei prodotti. Si veda anche, di Tommaso Ghidini, questa bella conferenza TED sul 3d printing spaziale. Nella prima parte si mostra, tra l’altro, la sezione di muro lunare stampata in 3d da D-SHAPE (Enrico Dini). |
||
Enrico Dini, nella sua presentazione al work-shop, mostra la tecnica di stampa 3d, mediante il grande plotter che “scrive” il legante chimico sugli strati di simulante della regolite lunare. Un altro tema molto dibattuto, nelle sessioni dedicate alle domande, quello del necessario coordi-namento tra università ed industria, che ASI sollecita fortemente, e per il quale intende sviluppare un centro di riferimento dedicato, che funga da stimolo e motore di comunicazione e collaborazione.
|
Un momento della presentazione di Enrico Dini, D-SHAPE.![]() |
||
Ovviamente, mi sentirei di aggiungere, una simile struttura, più che necessaria, potrà raggiungere gli obiettivi prefissati solo se saprà dotarsi di un setup analitico, capace di analizzare i punti di eccellenza di ogni azienda, ed andare oltre la logica dello “sportello”, muovendosi attivamente e continuativamente sia verso le aziende che verso le università. Fa ben sperare, da questo punto di vista, la positiva serie di incontri con le aziende che già vediamo in atto, da parte dell’agenzia. Additive Manufacturing: una scheda tecnica veloce e non esaustiva Qualche nota informativa è d’obbligo, poichè non tutti siamo esperti di tecniche produttive industriali. È abbastanza semplice. Le tecnologie tradizionali di fabbricazione meccanica si dicono sottrattive, perchè perlopiù lavorano i metalli per sottrazione di materiale: da un tondino, o da un pezzo squadrato, viene eliminato il materiale superfluo, mediante ad esempio la tornitura o la fresatura, supportate da tecniche CAD/CAM. Mi perdonino gli esperti delle tecnologie di lavorazione meccaniche per l’estrema semplificazione, ma è tanto per dare un’idea. La fabbricazione additiva, comunemente conosciuta anche come stampa 3D, opera al contrario, aggiungendo materiale dove serve, per mezzo di stratificazioni successive, modellate seguendo un disegno a computer (CAD/CAM). I materiali di partenza sono polveri metalliche o di altra natura, che possono essere opportunamente mescolate ad additivi, per ottenere leghe e materiali compositi. Le polveri vengono fuse mediante laser o altre metodologie comunque basate sulla concentrazione di calore, seguendo il profilo del modello elettronico. La stampa 3D viene anche utilizzata per creare oggetti a partire da polimeri o leghe polimeriche. L’additive manufacturing di precisione si articola in alcune sotto-tecnologie. Mi sia consentito di limitarmi qui ad elencare quelle che sono riuscito a captare: EBM (Electron Beam Melting), DMLS (Direct Metal Laser Sintering), SLM (Selective Laser Melting), SLS (Sinterizzazione Laser Selettiva), LBW (Laser Beam Welding), FDM (Fused deposition modeling). La stampa 3d a larga scala, presentata dal suo inventore Enrico Dini (D-SHAPE), utilizza sabbie combinate con leganti chimici, per ottenere un composto simile alla roccia, per la costruzione di strutture abitative ed elementi di varia natura, comprese barriere coralline artificiali, per la ripopolazione di fondali marini. Fin dal 2010 tale tecnologia viene sperimentata, in ambito ESA, anche nella prospettiva di “stampare” moduli abitativi sulla superficie lunare, utilizzando la regolite come materiale base di costruzione (si vedano anche i famosi video dell’architetto Norman Foster, uno dei partner del team D-SHAPE). Come è stato ampiamente discusso durante il workshop, si tratta di tecnologie destinate a cambiare radicalmente il modo di produzione industriale, o forse si potrebbe dire ad incarnare concretamente il modo di produzione post-industriale, se per produzione industriale si intende la fabbrica tayloristica seriale, anche nelle sue versioni più moderne, le isole robotiche. Ovviamente le catene produttive seriali continueranno ad esistere, per le grandi produzioni di massa. Ma l’aspetto importante è che sembra essere finito, o almeno significativamente ridimensionato, il paradigma delle economie di scala “più grande il volume più basso il costo di produzione”. Le stampanti 3D permettono infatti di abbassare drasticamente i costi di produzione anche per piccole o piccolissime serie. I vantaggi della produzione additiva, rispetto alla sottrattiva, sono moltissimi e, come è stato rilevato nel corso del workshop, non sono ancora stati scoperti tutti. Con l’additive manufacturing si possono ottenere geometrie e proprietà strutturali che sarebbero impossibili da raggiungere con i processi tradizionali. È possibile ottenere parti di elevatissima complessità geometrica. Viene inoltre enormemente ampliata la possibilità di personalizzazione della produzione, anche per bassi volumi. La stampa 3D permette una diminuzione drastica del numero di parti che compongono un oggetto, se non, in molti casi, la produzione in blocco unico. I tempi di prototipazione e produzione sono molto inferiori, rispetto alle tecniche tradizionali. Il prodotto finito presenta molta maggiore solidità, resistenza e compattezza, grazie alla sostanziale assenza di stress meccanico, che nelle lavorazioni classiche si deve a processi “violenti”, come ad esempio la tornitura, la fresatura, la piegatura. Si ha inoltre un sostanziale alleggerimento dei pezzi prodotti. Ultimo, ma non per importanza, l’additive manufacturing si presenta decisamente come tecnologia “verde”, o se preferite, sostenibile. Il risparmio di materiale e la riduzione degli sprechi sono enormi, se si pensa che le polveri non utilizzate dal processo non vengono in alcun modo rovinate nè modificate, quindi possono essere reimmesse nel processo per un numero elevatissimo di cicli. Allo stesso tempo si ha una drastica riduzione dell’inquinamento ambientale, sia dal processo di fabbricazione, sia dalla massiccia riduzione delle attività di trasporto nei vettori logistici, sia dal risparmio di materiale. Rispetto alla fonderia classica, si ha minore impiego di energia, e nessuna produzione di sostanze tossiche (diossine, ecc..). La meccanica non è più “meccanica” Come osservato da diversi oratori del workshop, ed in particolare dal prof. Quadrini, dell’Università Tor Vergata, le forme degli oggetti sviluppati mediante AM si discostano decisamente dalle forme, squadrate o rotonde, dei prodotti meccanici tradizionali, per avvicinarsi alle forme della natura: le ossa, gli alberi, le conchiglie. Mediante opportuno studio delle caratteristiche strutturali di certe forme naturali sarà quindi anche possibile ottenere componenti stampati in 3d con caratteristiche di robustezza e flessibilità paragonabili. Per chi possiede sensibilità artistica, le forme stampate in 3d sono decisamente intriganti, e non è difficile immaginare una stagione che potrà ispirare gli artisti almeno quanto lo fece il binomio futurismo-meccanica nei confronti dei grandi movimenti artistici del secolo scorso. Dimentichiamo termini come travi, staffe, pilastri, in favore di parole un po’ inquietanti, perchè risuonano con la nostra stessa biologia, come ad esempio la trabecola, che lasciano intravedere forse future contaminazioni tra scienza medica ed ingegneria meccanica, e non solo su terreni di incontro ovvi, quali la robotica e la cibernetica. L’AM e lo sviluppo spaziale Fin qui, si è parlato di una nuova tecnologia, certamente rivoluzionaria e decisamente rinascimentale, ma altrettanto decisamente terrestre. L’additive manufacturing, è stato ancora il prof. Quadrini ad osservarlo, lavora per stratificazione, in verticale, grazie alla forza di gravità. È quindi fortemente limitata, almeno per ora, ad applicazioni terrestri. Solamente in pochi casi (Loredana Santo dell’Univ. Tor Vergata, Maurizio Romeo di BEAMIT), si è parlato di tecniche di stampa 3d in condizioni di microgravità, sperimentanbili a bordo della ISS. Perchè, quindi, il forte interesse dell’ESA e dell’ASI per questa tecnologia? In primo luogo, non dobbiamo dimenticarlo, il focus principale delle agenzie restano, almeno per ora, le attività satellitari, per quanto il clima stia fortemente cambiando, come testimoniato dal forte interesse manifestato dall’ESA per la Luna, dopo l’insediamento del nuovo Direttore generale Johann-Dietrich Wörner, e dallo stesso discorso tenuto dal prof. Roberto Battiston, presidente dell’ASI, in chiusura del workshop. Aspettiamo con ansia che questo promettente indirizzo si traduca in gare concrete, nel database EMIT, ma è già molto importante che l’ESA abbia dato inizio ad un grande outreach mediatico, su programmi di reale espansione. La produzione di componenti per mezzo di tecniche AM è già iniziata, ed in campo aeronautico componenti stampati in 3d ormai volano già da qualche tempo. In campo spaziale Space X già utilizza valvole stampate in 3d sui Falcon, mentre il motore Super-Draco si avvale di una camera di combustione interamente stampata in 3d. Le tecnologie additive, nello scenario attuale, promettono una significativa riduzione dei costi di lancio in tutte le componenti: dai lanciatori, che costeranno molto meno, ai carichi paganti (satelliti). Il tutto potrà essere disegnato, protipato e prodotto in tempi ridotti di almeno un ordine di grandezza, mediante tecnologie additive, peserà meno, costerà meno, tendenzialmente riducendo anche lo stringente requisito di elevatissima affidabilità dei componenti spaziali. Quando le missioni costavano un miliardo, era inevitabile insistere su tecnologie più che consolidate, a scapito dell’innovazione. Come fortemente sottolineto da Mauro Varetti, CEO dell’aggressiva startup torinese 3D-NT, le tecniche additive, abbattendo i costi, apriranno il settore aerospaziale alla sperimentazione, senza venir meno ai requisiti di affidabilità, in particolare quando le missioni includono esseri umani. Tutto questo, ovviamente, non sarebbe forse nemmeno immaginabile, se Elon Musk non avesse abbattuto il costo dei lanci dallo standard dei 900 milioni, mantenuto — cartellisticamente — dalla United Launch Alliance per tanti anni, a 60 milioni, anche prima dell’avvento dei razzi interamente riutilizzabili. E, quando il processo di riutilizzo sarà consolidato, il costo di lancio si attesterà intorno ai 500 mila dollari. Le potenzialità dell’additive manufacturing, per lo sviluppo dell’astronautica civile Le potenzialità dell’AM sono ancora maggiori. Tendenzialmente la messa in orbita di satelliti potrebbe ridursi quasi a zero, almeno per la componente del lancio da terra. |
|||
Il Presidente dell’ASI Prof. Roberto Battiston, in chiusura del workshop, ha voluto raccogliere, in un certo modo, la sfida di Space X e della NASA. Ha infatti ipotizzato che, grazie all’enorme riduzione del costo dei motori a razzo dovuta alle tecnologie additive, i razzi spendibili possano addirittura in futuro rivelarsi più convenienti, rispetto a quelli riutilizzabili. Quello che è certo è che potenti forze rinascimentali sono ormai lanciate: i razzi riutilizzabili di Space X, e le tecnologie di fabbricazione additiva. Entrambe queste forze stanno abbattando il muro, che sembrava invalicabile fino a poco tempo fa, dell’elevato costo del trasporto da terra all’orbita bassa. E questo, da qualsiasi parte lo si guardi, aprirà la frontiera alta a molte iniziative private imprenditoriali, di tipo industriale, turistico, di servizio. |
Roberto Battiston – ASI![]() |
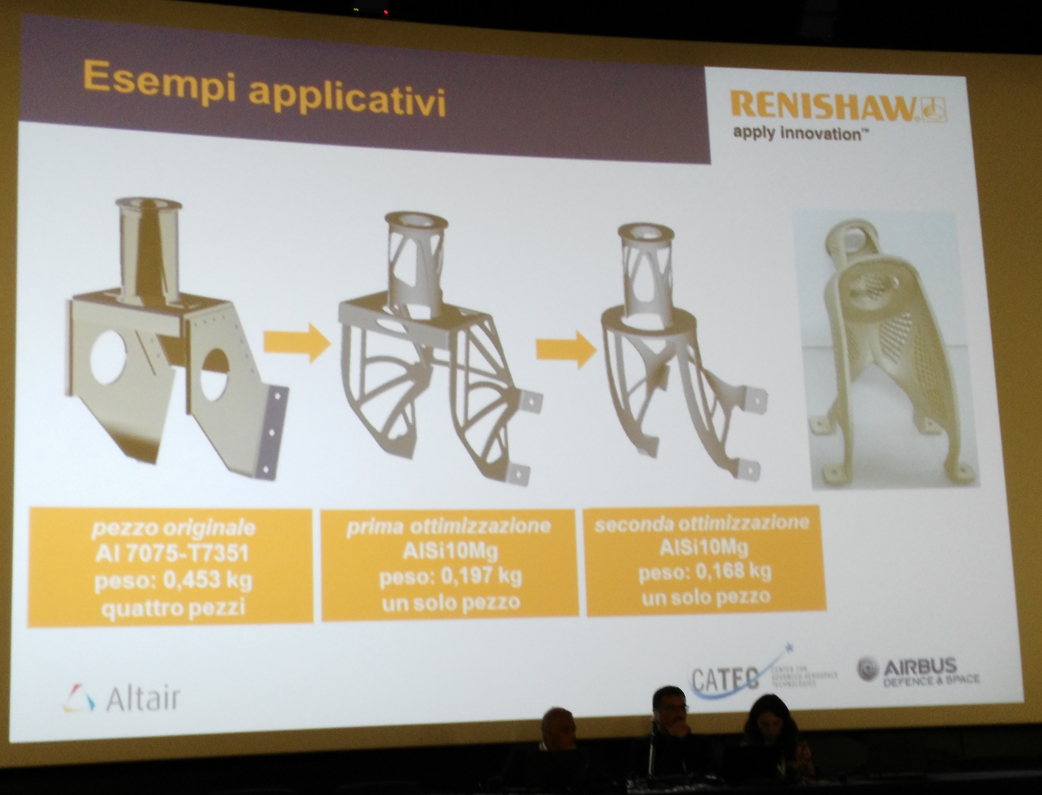
Additive manufacturing: un’alternativa ai razzi riutilizzabili?
Pensavate possibile, nel contesto di questa crisi che sembra non finire mai, che potesse esistere un settore industriale, anche nel nostro paese, che cresce a due cifre? Bene, questo settore esiste, e si chiama additive manufacturing o, per dirla in italiano, fabbricazione additiva.
Un breve resoconto, ed alcune considerazioni, sul workshop Additive Manufacturing, organizzato dall’ASI, dal 20 al 22 Luglio, nell’auditorium della sede di Tor Vergata a Roma. L’iniziativa, che ha visto fortemente impegnati Roberto Formaro (capo della Technology and Engineering Division dell’ASI), Danilo Rubini ed il loro staff, è stata decisamente un successo, ed ha visto la presenza, nei tre giorni, di più di trecento partecipanti, in grande maggioranza appartenenti al settore industriale ed al mondo accademico. L'additive manufacturing si sta affermando come una tecnologia decisamente rinascimentale.